Bored cast-in-place piles have the advantages of low construction noise, and low vibration, pile length and diameter can be freely changed according to design requirements, pile tips can reliably enter the bearing layer, and a large single pile bearing capacity is large. However, from the beginning of drilling to the end of pile formation, quality problems or even quality accidents are easily caused due to the influence of many factors. Therefore, quality control has become a difficult point in construction.
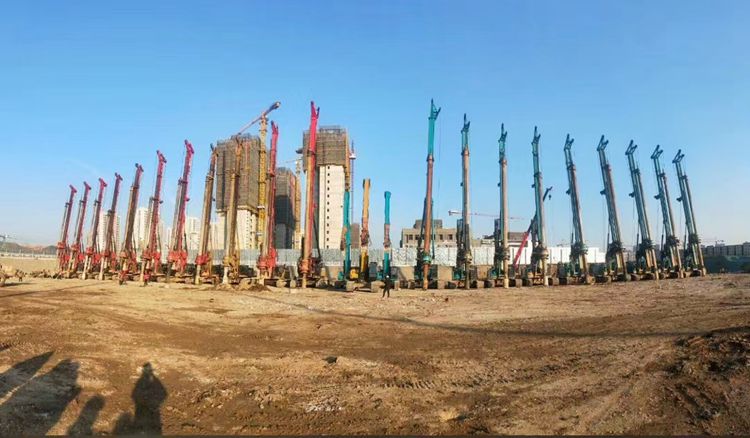
Analysis of Causes Affecting Pile Quality
Analysis of the causes affecting the strength of the upper part of the column
(1) According to the construction specifications, the silt at the bottom of the hole must be completely removed after drilling. However, during the actual construction process, it is difficult to remove the silt completely. Therefore, when the first bucket of concrete was poured for bottom sealing construction, the sediment deposited at the bottom of the hole was Silt must be mixed into the concrete. Since the underwater concrete poured with the conduit is lifted from bottom to top, the concrete poured first rises above the hole, so it is easy for the upper section of the pile to have lower strength.
(2) When pouring concrete, if the conduit is inserted too deep into the concrete and the pouring speed is fast, more aggregate will easily be deposited deep in the hole. In addition, the segregation of concrete caused by the vibration process will also easily lead to The quality problem of the lower strength of the upper part of the pile body.
(3) The soil around the buried casing is not dense, the water level difference in the casing is too large, or the drill bit collides when it rises and falls, causing quality problems.
(4) The main reasons for hole wall collapse are loose soil, poor mud wall protection, failure to seal the casing tightly with clay, and low water level in the casing. Too fast drilling speed, too long dry drilling time, too long waiting time for filling after hole formation and too long filling time will also cause hole wall collapse.
(5) The installation stability of the drilling rig is poor, which is caused by unstable installation of the drilling rig or bending of the drill pipe during operation. The ground is soft or uneven, the soil layer is distributed obliquely, or there are large boulders or other hard objects in the center of the soil layer, etc., which may lead to large vertical deviation or bending of the pile hole after the hole is formed.
(6) The hole cleaning is not clean or secondary cleaning is not carried out; the specific gravity of the mud is too small or the amount of mud injected is insufficient, making it difficult to float the sediment. During the lifting process of the steel cage, the hole position is not aligned and the hole wall collides with the soil, causing the soil to collapse. After placing the bottom of the pile and clearing the hole, the time for irrigation is too long, resulting in mud deposition and even excessive sediment at the bottom.
Reasons Affecting the Quality of Other Pile Bodies
(1) During the concrete pouring construction, if the conduit is inserted into the concrete too shallowly (less than 1.5m), the concrete will not rise during the pile formation process but will be paved. At this time, the mud and mud blocks will Be easy to mix into the concrete, thus affecting the quality of the pile body. In addition, if the designed diameter of the pile body is too small, the concrete will be restricted by the hole wall when it is turned up, resulting in cavities and honeycomb defects in the pile body.
(2) The bearing capacity of bored piles is mainly manifested by pile circumferential friction, and pile circumferential friction is closely related to the shape of the hole wall and the quality of the retaining wall. During the construction process, the shape of the hole wall is determined by factors such as the rotation speed of the drill bit, the descent speed of the drill pipe, and the soil quality. The better the mud performance (including bulk density, viscosity colloid rate, sand rate, and other indicators), and the higher the elevation, the better the performance. If the retaining wall is well protected, the friction around the pile will be greater, but the construction will be more difficult and the cost will increase accordingly.
(3) In the entire process of drilling holes, removing drill pipe mud, stopping circulation, hoisting steel cages, and pouring underwater concrete, there are many construction links and a long time, which will cause thicker silt to accumulate at the bottom of the hole and affect the results. Pile quality. The longer it sits, the more silt will accumulate.
(4) During the process of pouring concrete underwater, its fluidity, initial setting time, and cohesion properties will become worse. If there is a little negligence, it is easy to produce cavities, honeycombs, segregation, mud inclusions, and even broken piles. defect.
Pile Quality Control
Measures to Ensure the Strength of the Upper Section of the Pile
(1) Based on the diameter of the pile and the concentration at the bottom of the pile, correctly determine the volume of the first bucket of concrete. Generally, it can be 1.5~2.0m³, or it can be controlled according to 10% of the design volume of the pile body.
(2) The pile quality is related to the pouring height of the pile body. Generally, the pile height is controlled to be 0.5~1.0m higher than the designed pile top elevation. After the elevated part of the concrete is chiseled away, there should be no laitance or mud in the remaining part, and the concrete markings should meet the design requirements, otherwise, it will have to be reworked and poured again.
(3) The length of the conduit inserted into the concrete should be appropriate, generally 2~6m and long piles can be increased accordingly.
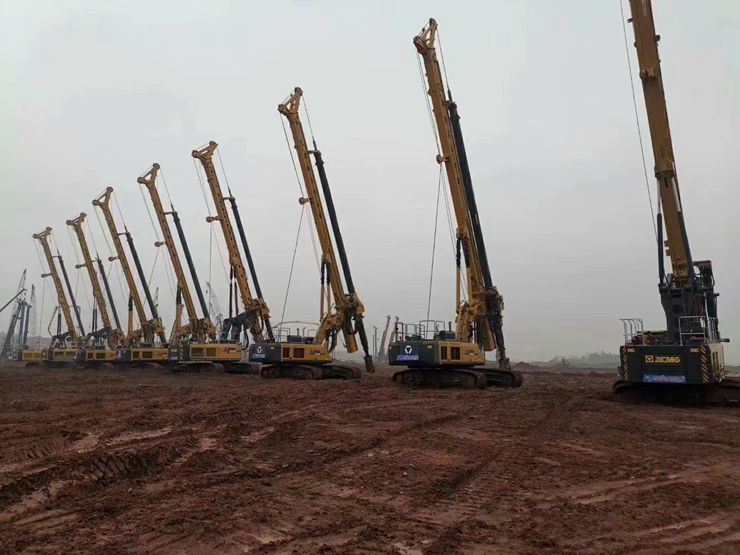
Measures to Ensure the Quality of the Pile Body
(1) Before construction, more than 2 test holes should be made. By testing the bore diameter, verticality, hole wall stability, hole bottom sedimentation, and other indicators, it is used to check whether the selected equipment and process methods meet the technical requirements. When testing, the stability time of the hole wall should be less than 12 hours, and the number of tests should be less than 2. For some important projects, the number of diameter measurements may be increased accordingly depending on the situation.
(2) The mud used for protecting the wall should meet the requirements for protecting the wall. The liquid level needs to be more than 0.5m above the groundwater level. If conditions permit, it is better to be more than 2m above the groundwater level. If the mud colloid ratio of the protective wall is low and the sand ratio is high, not only will the performance of the protective wall be poor, but also due to its large bulk density, the problem of excessive sedimentation speed will inevitably occur. Generally speaking, when holes are formed in clay or sub-clay soil, clean water can be injected to use the original soil to form a slurry to protect the wall, and the relative density of the ballast mud is controlled to be between 1.1 and 1.2; when holes are formed in sandy soil or thick sand-filled soil When forming holes in the layer, the relative density of the mud should be controlled between 1.1 and 1.3; when forming holes in sand mixed with pebbles or soil layers that are prone to collapse, the relative density of the mud should be controlled between 1.3 and 1.5. During the construction process, the relative density, viscosity, sand content and colloid rate of the mud should be measured frequently to ensure that the relative density of the mud within 500mm of the hole bottom before pouring is less than 1.25, the sand content is greater than 8%, and the viscosity is less than 28 Pa·s. For some small-diameter piles less than 1m in diameter, a reasonable mud level must be maintained in the hole even when the mud circulation stops.
(3) During the period before concrete pouring, the stability of the hole wall must be ensured, and no necking or hole wall collapse occurs. To ensure that the thickness of the sediment at the bottom of the hole meets the technical requirements of the specification (end-bearing piles are not more than 50mm, friction end-bearing piles and end-bearing friction piles are not more than 100mm, and friction piles are less than 300mm), so as not to affect the bearing capacity of the piles. After drilling to the designed bearing layer, the mud must be cyclically diluted to reduce the relative density and remove suspended sand and gravel in the mud. In addition, a vacuum pump must be used to extend through the pipe to the bottom of the pile to suck out the end sediment. If the requirements are strict, the slag suction treatment must be carried out after placing the steel cage and before lowering the conduit.
(4) The steel cage hoisted into the hole must not collide with the wall hole or be deformed or damaged. After hanging, first fix the steel cage in a vertical position, and then clean the hole for the second time to check the thickness of the silt at the bottom of the hole. Once it meets the regulations, concrete pouring construction will start within 0.5 hours.
(5) The diameter of the water-proof pick-up used should match the inner diameter of the conduit, and at the same time have good water-proof performance to ensure smooth discharge. When pouring concrete, the control of concrete mixing time and concrete slump should be strengthened. Underwater concrete must have good workability. The mix ratio should be determined in the laboratory. The slump should be 18~22cm. The maximum particle size of coarse aggregate should not be larger than 1/4 of the diameter of the conduit and the minimum clear distance of the main bars of the steel cage. , and should be less than 40ram. In order to improve the workability and retardation of concrete, underwater concrete should be mixed with admixtures. The sealing of the conduit connection part should be ensured. The conduit should be assembled and pressure tested before use. The water test pressure should be 0.6~1.0MPa to avoid water intrusion into the conduit. During the concrete pouring process, concrete should be slowly poured into the funnel’s conduit to avoid the formation of a high-pressure air lock in the conduit. During the construction process, mechanical equipment should be monitored at all times to ensure normal operation of the machinery and avoid mechanical accidents.
(6) After the hole is formed, the hole must be carefully cleaned, usually with flushing fluid. The punching time should be determined according to the sediment in the hole. Concrete must be poured in time after punching to avoid the sediment at the bottom of the hole exceeding the specifications. Before pouring concrete, carefully measure the hole diameter to accurately calculate the base hole and the first concrete pouring amount. During the concrete pouring process, the elevation of the concrete surface and the burial depth of the conduit should be controlled at all times. The lifting conduit must be accurate and reliable, and the operating procedures must be strictly followed. Strictly determine the mix ratio of concrete. The concrete should have good workability and fluidity, and the slump loss should meet the pouring requirements. In areas with large groundwater activity, casing or cement must be used for treatment in advance. Concrete can be poured only after the water is stopped successfully. Concrete should be poured from the conduit. The pouring process is required to be continuous and rapid, and the amount of concrete to be poured must be sufficient. During the concrete pouring process, power outages and water outages should be avoided. The iron wire binding the cement water-proof plug should be determined according to the amount of concrete poured for the first time to prevent breakage. Ensure the sealing of the conduit. The disassembly length of the conduit should be determined according to the rising height of the concrete inside and outside the conduit. Do not pull out too much.