Classification of Piles
1. Score according to the number of piles
Single pile: only one pile
The row of piles: a row of multiple piles
Pile group: multiple rows of piles
2. According to location
Underwater pile: The pile is underwater
Water pile: The pile position is above the water
3. According to the making method
Prefabricated piles: piles that are prefabricated and then driven into place
Cast-in-place pile: A pile that is first formed into holes and then poured into shape
4. Divided according to pile construction methods
Manually dug piles: manually excavated holes and then piles
Bored cast-in-place piles: Use a drilling rig to drill holes and then form piles
Driven piles: drive prefabricated piles into the foundation. Prefabricated piles include wooden piles, steel pipe piles, reinforced concrete piles, PHC piles, etc.
5. Divide according to pile formation method
Non-squeezing soil pile: does not squeeze the soil on the side of the pile
Partially squeezed soil pile: partially squeezed pile side soil
Soil squeeze pile: The pile squeezes the soil on the side (bottom) of the pile
6. Divided according to force characteristics
Friction pile: The pile top load is entirely borne by the pile side resistance.
End-bearing friction pile: The pile top load is mainly borne by the pile side resistance.
End-bearing pile: The pile top load is borne by the pile end resistance
Friction end-bearing pile: The pile top load is mainly borne by the pile end resistance.
7. According to the use function of piles
Compression pile: bears the pressure from the top of the pile (usually)
Vertical pull-out pile: the pile bears an upward pulling force
Horizontally loaded piles: The pile head bears horizontal loads
Composite loaded piles: piles bear composite loads
8. According to the cross-sectional shape of the pile
Round pile: The pile has a circular cross-section (pipe piles are hollow)
Square pile: The cross-section of the pile is square
Special-shaped piles: piles with round-ended, oval, or polygonal cross-sections, etc.
9. According to the spatial position of the pile length direction
Vertical pile: The axis of the pile is a vertical line
Horizontal pile: The axis of the pile is a horizontal line
Inclined pile: The axis of the pile forms a certain angle with the horizontal line
10. According to the shape of the pile length direction
Piles of equal cross-section: piles with the same cross-section within the length of the pile
Variable cross-section piles: piles with different cross-sections within the length of the pile
Construction of Commonly Used Pile Foundations
1. Common highway bridge pile foundation construction methods
Manually dug piles: suitable for water or in strata with small water seepage. The holes are dug manually and then piles are formed.
Bored cast-in-place piles: Suitable for underwater or stratum with large water seepage. Mechanical equipment such as impact drilling rigs, impact drilling rigs, rotary drilling rigs, rotary drilling rigs, etc. are used to drill holes and then form piles.
Driving piles: Diesel piling hammers or vibrating piling hammers are often used to drive prefabricated steel pipe piles to support platforms or trestles; PHC piles are driven into pile foundations for bridges.
2. Manual digging pile construction
Scope of application: dry areas, relatively stable strata
Construction preparation: Verifying drawings, writing construction plans and details, technical briefings, site leveling and setting out, preparing materials, equipment, concrete mix proportions, construction water, electricity, roads, communications, personnel, etc.
Hole digging equipment: storage hopper, hoist, hoisting rope, fan, ladder, mixer, vibrator, inner formwork of the protective wall, strong lifting safety rope, safety helmet, protective device, etc.
Hole digging construction: Dig down to the design depth section by section.
Construction safety precautions:
Workers who go under the hole must fasten their safety belts and hang up the strong safety rope fixed on the hole mouth; if there is water seepage in the hole, it must be pulled out in time; if there is harmful gas in the hole (regular testing), animal testing must be carried out before operating, and provide air for ventilation promptly; communicate with the personnel in the hole at all times, and in case of emergency, use a strong safety rope to rescue the personnel in the hole; when lifting slag and lowering the hopper, workers in the hole should stop construction and under protective cover.
Installing the steel cage: After digging the hole, the crane and other equipment will be used to install it in sections until completion.
Concrete pouring for the pile body: When the pile body is dry, use a string tube to inject concrete into the hole (to prevent segregation) into the place to be poured and vibrate it tightly; when there is a lot of water, use the method of pouring underwater concrete for construction.
3. Construction of bored piles
1) Scope of application: Suitable for the construction of foundation piles under water or in various strata with large water seepage
2) Drilling methods: hole drilling with impact drill, hole drilling with punching drill (not commonly used now), hole drilling with rotary (swivel) drilling rig, hole drilling with rotary drilling rig
3) Impact drilling rig hole construction
Construction preparation: verify drawings, prepare construction plans and details, technical briefings, site leveling and setting out, preparation of construction platforms, casings, water, electricity, roads, communications, and lifting and transportation equipment, determination of concrete mix proportions, and selection of drilling rigs and drill bits. Field, clay, gravel preparation, personnel, etc.
Drilling: The slurry is made by throwing high-quality clay and impacting the slurry in the hole.
The mud indicators are specific gravity 1.15~1.25, viscosity 16~17s, and pH value 6.5. Connect all the casings with slots at the top (pile group), and use the undrilled holes as sedimentation tanks.
When drilling: the stroke should be small, the slag should be sucked frequently, and the inspection and measurement should be frequent, to prevent the drill from getting stuck, falling out, and hole deviation during the drilling process. It is strictly forbidden to use the empty hammer. At the same time, construction records should be kept, and if the actual rock formation changes are inconsistent with the design, report them to the relevant departments promptly.
Final hole inspection: When the drilling reaches the designed final hole elevation, check the hole depth, hole diameter, hole position, and hole shape, then fill in the final hole inspection certificate, and promptly notify the supervision engineer to come to the site for inspection and acceptance.
4) Rotary drilling rig hole construction
Construction preparation: verify drawings, prepare construction plans and details, technical explanations, site leveling and setting out, construction platform, casing, materials, equipment, water, electricity, roads, communications, personnel preparation, concrete mix ratio determination, drilling rig (forward and reverse) circulation), drill bit selection and entry, mud preparation, etc.
Drilling: Drilling in sand layers, and mud quality is the key to the success or failure of drilling. During the entire drilling process, various technical indicators of the mud must be strictly controlled.
During the drilling process: high-quality bentonite and external additive Na2CO3 are used to make slurry (about 3%). When drilling into a sand layer, the amount of grout added is about 2 times the unit volume drilled. When drilling into a rock formation, the amount of grout added is 1.0-1.2 times the unit volume depending on the completeness of the rock formation.
Strictly control the viscosity: 19-21s in the sand layer and about 19s in the rock layer. The final hole time is 19 seconds. At this time, the specific gravity is controlled to 1.06-1.10t/m3, and the sand rate is reduced to about 1%. During the entire process of drilling and clearing holes, qualified mud should be filled into the holes. Except for rock formations that can make mud, clean water is generally not allowed to be put into the holes.
Overpressure head: During the entire process of drilling and cleaning, the overpressure head in the hole is always maintained at 2.0-2.5m.
Two times of hole cleaning: both use the pulp extraction method to clean the hole.
When drilling to the required hole bottom elevation, lift the drill bit 15cm away from the hole bottom, and use the drilling rig’s gas lift reverse circulation to clean the hole for the first time, usually 2-3 hours. When all mud indicators are qualified, especially the sand rate, The hole clearance in the rock formation should be reduced to less than 1% before drilling begins.
Before pouring underwater concrete for secondary hole cleaning, a φ57×3m steel pipe is inserted into the concrete conduit as an air duct to form an air suction machine to clean the hole. A hose is connected to the conduit to discharge the hole-cleaning mud into the circulation hole casing (sedimentation Pool), and then enter the construction hole circulation after settling. The floating crane lifts the conduit and moves it inside the casing to clean the sediment at the bottom of the hole. After checking that the sucked-out mud and hole depth meet the requirements, the hose and air duct are removed, a funnel is installed, and underwater concrete pouring begins.
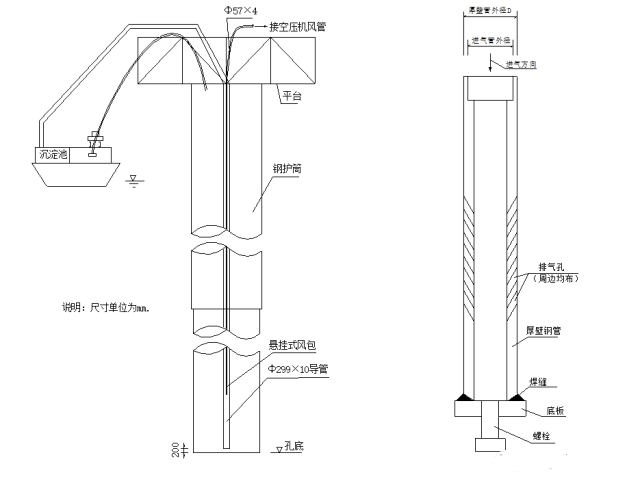
Hole inspection: After the hole is formed, use a (DM-686III type) ultrasonic wall measuring instrument to detect the diameter of the hole, the inclination of the hole wall, and the flatness of the hole wall.
From top to bottom of the hole wall, the ratio of the offset value of the vertical scribed line to the hole depth is the slope ≤ 1% and the offset value of the actual hole is 0.3%-0.5%. The flatness of the local hole wall does not meet the requirements, and the hole scanning process is used to pass.
5) Drill the hole with a rotary drilling rig
Construction preparation: verify drawings, prepare construction plans and details, technical briefings, site leveling and setting out, construction platforms, casings, materials, equipment (concrete mixing and transportation, steel bar fabrication and installation, etc.), construction water, electricity, roads, communications, and personnel preparation, the concrete mix ratio is determined, the drilling rig and drill bit are selected and put into operation, and the wall protecting mud is prepared.
Drilling: Rotate bucket by bucket to extract soil to form a hole until the bottom of the pile, and at the same time, replenish qualified wall-protecting mud in the hole.
Inspection holes: Inspect holes after drilling is completed. After meeting the requirements, wait for the steel cage to be installed.
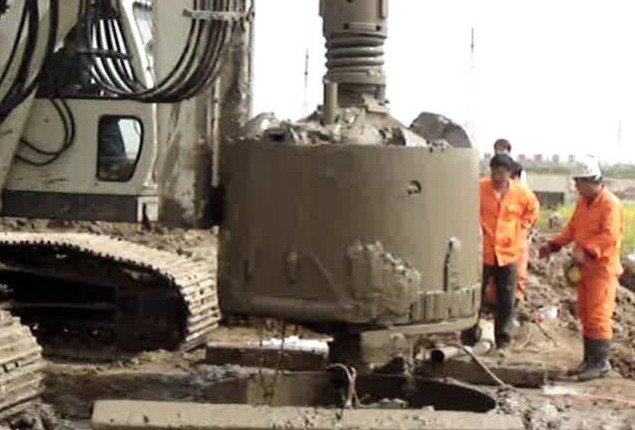
6) Steel cage installation
The steel cage frame adopts extrusion joints or straight threaded joints. Each steel cage frame is made in sections and molded. Each section is 9.0m (12.0m) long. It is lifted by a crane, spliced at the hole, and placed into the hole;
For holes drilled by a rotary drilling rig, the steel cage frame should be pre-made in sections near the pile location and spliced together. It can be placed as soon as possible after the hole cleaning is completed, and concrete should be poured into the pile (anti-collapse hole) as soon as possible.
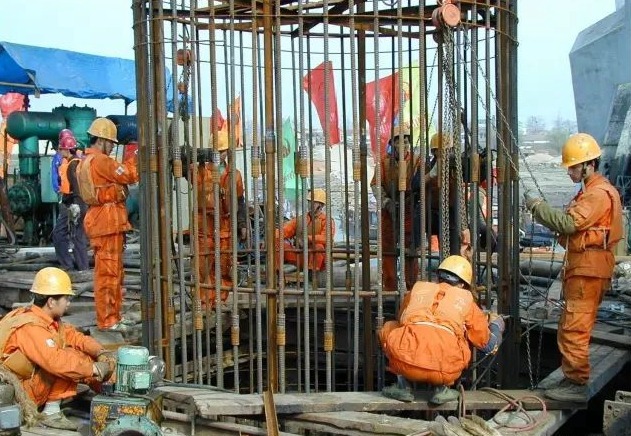
7) Pouring foundation pile concrete
Pouring underwater concrete into piles: Make preparations in advance for materials, mixing stations, mix ratio trial and verification, storage tanks, conduits, and pre-inspection. The concrete (retarded setting time is about 15h, slump 18-22cm) meets Require. The conduit uses φ299×10mm seamless steel pipe and a quick thread connector. The ball-driving method is used to pour concrete into the bottom seal. The distance between the conduit and the bottom of the hole is 0.3m-0.4m. The thickness of the concrete in the hole after sealing is more than 2m, and the conduit is buried in the concrete for more than 1.0m. During the pouring process, the buried depth of the conduit is always maintained between 2-6m.
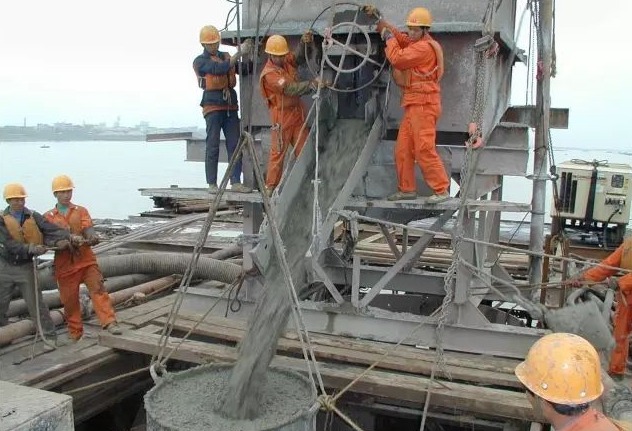
8) Pile inspection
Quality inspection of completed piles: To detect the quality of bored pile concrete, all ultrasonic non-destructive inspections are used. The owner and contractor respectively entrust qualified professional inspection units to conduct inspections (for extra large bridges, 5% of the total amount of drilled cores will be drilled for core damage inspection). If the test results are all qualified, the grouting in the test pipe and the foundation pile construction will be completed; otherwise, the treatment should be carried out until it is qualified.
4. Driving pile construction
Scope of application: Generally used for underwater foundations (except for housing construction)
Driving piles: Diesel piling hammers or vibrating piling hammers are often used to drive prefabricated steel pipe piles to support platforms or trestles; PHC piles are driven into pile foundations for bridges; prefabricated reinforced concrete piles are driven into foundations for houses. Base.
Common Quality Problems and Solutions in Pile Foundation Construction
1. Hole collapse
It is divided into collapse holes during hole formation, collapse holes after hole formation, and collapse holes when pouring concrete.
If the hole collapses when the excavation encounters quicksand strata, measures such as shortening the height of each section of the protective wall, properly driving piles into the soil, and adding accelerating admixture to the concrete of the protective wall can be used to stabilize the protective wall as quickly as possible.
If the hole collapses during drilling, measures such as re-creating the hole wall (punching), increasing the qualified mud concentration, increasing the overpressure head, and filling part of the concrete (slab stone) can be adopted.
If the hole collapses after being formed, the hole should be re-formed after cleaning. Construction should be reasonably organized to ensure the continuity and timeliness of process connections (especially rotary pile excavation) and reduce the chance of hole collapse.
If the hole collapses when pouring concrete, stop pouring immediately and clean the hole before pouring again or re-hole the hole before pouring.
2. Dropping objects
When drilling in the rock formation (Ehuangqiao case), due to the slippage of the drill pipe joint, the drill bit (including two drill rods) fell into the hole. Use a special overshot to insert the drill rod and lift the drill bit out of the hole; During the inspection, I found that the drilling rig was vibrating violently. I pulled out the drill bit and found that two hobs fell off and fell into the hole. I used an electromagnet to suck them out.
3. Drill stuck
The uneven softness and hardness of the formation causes the hammer to get stuck (during punching), the hammer sticks or the hammer head is enlarged and punched quickly. It is processed by filling stones, enlarging the hammerhead, and then filling again.
4. Buried drill
After the hole is collapsed and the drill is buried, the collapsed material above the buried drill point is sucked out, and then the drill bit is lifted out.
5. Drilling holes leaking slurry
If it is found that the water head in the hole cannot be maintained, it is analyzed that slurry leakage has occurred, which is caused by insufficient burial depth of the casing, poor wall protection, water leakage when encountering caves, or rock formation fissures. Use a vibrating hammer to sink the steel casing to a certain depth, insert the inner casing, repeatedly create holes to protect the walls, or fill the holes with concrete. After drilling is resumed, the water head can be maintained for normal drilling.
6. Drilling deviation
Due to the large inclination of the rock surface at the pier location, uneven rock formations, weak layers, and faults in the middle, the drilling is prone to deflection. Due to the inclination of the borehole, the main manifestation is local curvature in the middle section of the rock layer, and the treatment method depends on the specific situation. If the inclination is not serious, the local area will be repeatedly scanned. If the inclination is serious, underwater concrete will be poured 50cm above the rock surface elevation. When the concrete strength reaches 25MPa, drilling will be restarted and the footage will be slowed down. After treatment, the drilling inclination can reach the requirement of ≤1%.
7. The steel cage cannot be lowered into place
If the holes are inclined, shrinkage holes, the cross-section of the holes does not meet the requirements, or the steel cage is not straight, etc., use sweeping holes or straighten the steel cage to enable the steel cage to be lowered into place.
8. Catheter blockage
Concrete has poor workability, pipe leakage, and things stuck in the pipe, etc. Adjust the properties of the concrete, seal it to the pipe, and remove stuck things in the pipe to achieve smooth pouring.
9. Move the steel cage upward
The buried depth of the conduit is too large, causing the steel cage to lift up when the concrete is turned up, or the steel cage is not firmly fixed. Use a reasonable buried depth of the conduit to deal with it. If it is discovered after the pile is completed, consult with the designer before dealing with it.
10. The steel cage suddenly fell
After the steel cage is installed in sections, the steel rope suddenly breaks during lifting, or the steel cage is not firmly fixed. Sometimes it is accompanied by safety accidents (the workers working in the steel cage of a certain bridge were tied with safety ropes hanging on the steel cage, and when the steel cage fell, they were carried into the hole and drowned). Therefore, reasonable and reliable equipment for stabilizing and lifting the steel cage must be used, and workers must not enter the cage.
11. The acoustic tube cannot be used normally.
Caused by slurry leakage or deformation in the pipe. The pile body is inspected by clearing the leakage slurry in the pipe or re-drilling the core hole instead of the acoustic detection pipe.
12. The quality of concrete on the pile body is unqualified
The acoustic test results of the pile body showed that the concrete was defective and the pile quality was poor. Most of them are sediment at the bottom of the hole, concrete separation, insufficient concrete strength (top of the pile), leakage of the conduit, unprocessed conduit lifting (broken pile), excessive burial depth of the conduit, not placing the conduit in the center of the hole, and conduit re-opening after balling. It is caused by the formation of closed pores during pouring, collapse holes that were not discovered when pouring piles, mechanical failure during pouring of piles that did not complete the pouring of piles (broken piles), shrinkage holes, or runoff water passing through the pile body during pouring of piles, etc.
1) Concrete defects at the bottom of the hole
The acoustic test result of the pile body showed that the concrete at the bottom of the pile was defective, indicating that there was sediment at the bottom of the hole or that the concrete bottom seal was not successful when pouring the pile. The grouting treatment is carried out after drilling cleaning.
During construction, the holes should be carefully cleaned, and the concrete in the pile should be poured after meeting the specification requirements to ensure that a sufficient amount of first-pouring bottom-sealing concrete is continuously injected into the bottom of the hole.
2) Insufficient strength of pile top concrete
This is caused by inaccurate measurement of the height of the concrete pouring in the pile, the laitance being too thick, or the self-pressure water head in the hole not self-tightening enough. The poor-quality concrete at the top of the pile was removed and then poured again.
When the self-pressure water head in the hole is insufficient during construction, vibrating should be carried out, the hole cleaning quality should be strictly enforced, reliable depth-measuring equipment should be produced, and the relationship curve between pouring height and concrete quantity should be drawn. If there are any abnormalities, timely analysis and treatment should be carried out.
3) Concrete defects in the middle of the pile body
(1) Caused by water leakage in the duct
Water leaked from the conduit when pouring the piles, and the concrete poured after being washed was uneven and of poor quality. It should be checked at any time, analyzed in time, and dealt with immediately.
Pre-inspection work should be strictly carried out before construction, and pipe sections that do not meet the requirements shall not be used.
(2) The catheter is evacuated and not processed
Cause broken piles. The buried depth of the pipe should be accurately measured based on the height and quantity of concrete pouring, and reliable pipe lifting equipment should be used to lift the pipe to a fixed length.
Before construction, the length (height) of each section of the pipe should be accurately measured section by section, and recorded by a construction specialist, and the buried depth of the pipe should be strictly controlled within the range of 2-6m.
(3) The buried depth of the conduit is too large and the conduit is not placed in the center of the hole.
The buried depth of the conduit is large, resulting in the concrete in the new conduit being unable to uniformly lift the concrete poured in the entire section of the existing pile. The concrete in the new conduit will turn up along the path of small resistance. This is often the case during construction), it is more likely that the concrete cannot be lifted evenly. therefore. The concrete that is turned up along the path of least resistance covers the defective concrete that was previously on top, creating a defect there.
During construction, the buried depth of the conduit must be strictly controlled within the range of 2-6m.
(2) The catheter is evacuated and not processed
Cause broken piles. The buried depth of the pipe should be accurately measured based on the height and quantity of concrete pouring, and reliable pipe lifting equipment should be used to lift the pipe to a fixed length.
Before construction, the length (height) of each section of the pipe should be accurately measured section by section, and recorded by a construction specialist, and the buried depth of the pipe should be strictly controlled within the range of 2-6m.
(3) The buried depth of the conduit is too large and the conduit is not placed in the center of the hole.
The buried depth of the conduit is large, resulting in the concrete in the new conduit being unable to uniformly lift the concrete poured in the entire section of the existing pile. The concrete in the new conduit will turn up along the path of small resistance. This is often the case during construction), it is more likely that the concrete cannot be lifted evenly. therefore. The concrete that is turned up along the path of least resistance covers the defective concrete that was previously on top, creating a defect there.
During construction, the buried depth of the conduit must be strictly controlled within the range of 2-6m.
(6) Mechanical failure stops pouring when pouring piles
During the pile pouring, a mechanical failure occurred and the pile pouring was not completed (the pile was broken). The conduit was pulled out, the fault was resolved, and the pile was poured again.
The conduit should be pulled out in time, the top concrete should be sucked out, and it should be poured again when appropriate.
(7) Runoff water passes through the pile body
During the pile pouring process, there was flowing water flowing through the pile body, and the concrete was found to be defective after the pile construction was completed.
The piles above the defective section are chiseled out and redone (inside the rock).
During construction, the hole walls of the moving water runoff section can be protected first.
13. The pile position deviation exceeds the limit
The position of the pile hole was not rechecked after setting out, resulting in the deviation exceeding the limit after the pile was completed. When the overrun is small, it can be used after design verification and appropriate treatment; when the overrun is large, piles can be re-established after accurate setting out and review.
14. Cracks in the concrete of the pile body
After the construction of the pile body was completed, cracks were found in the pile body near the ground. It is mostly caused by the pile being subjected to lateral (soil) thrust.
The pile is reinforced after removing the thrust objects on the side of the pile. When the cracks are wide and the deformation is large, a special reinforcement and reinforcement treatment plan is proposed together with the design.
15. Pile body sinks
After the construction of the pile body was completed, it was found that the pile body had sunk, resulting in cracks in the column body or cover beam. This is mostly caused by the soft bottom of the pile and insufficient frictional resistance around the pile.
Work together with the design to study replace and reinforce the original piles by adding piles and other solutions.
Issues to Discuss
1. Lower the hole bottom elevation instead of cleaning the hole
This is never allowed. There will be serious adverse consequences if the aforementioned piles cannot reach the bearing capacity and sink after being stressed. The treatment is difficult and expensive.
2. Construction of piers without pile inspection
It is possible that the inspection pipe is not smooth, or the construction period is tight, and the subsequent piers are constructed without ultrasonic inspection of the pile body, resulting in a fait accompli that cannot be inspected, which is also absolutely unacceptable.
3. No report is made after the steel cage floats
It is impossible to cut it off yourself and hide the fact that the steel cage is floating. Once it is discovered that the steel cage is floating during the pouring of pile hole concrete, it should be reported in time and studied and dealt with.
Thank You!