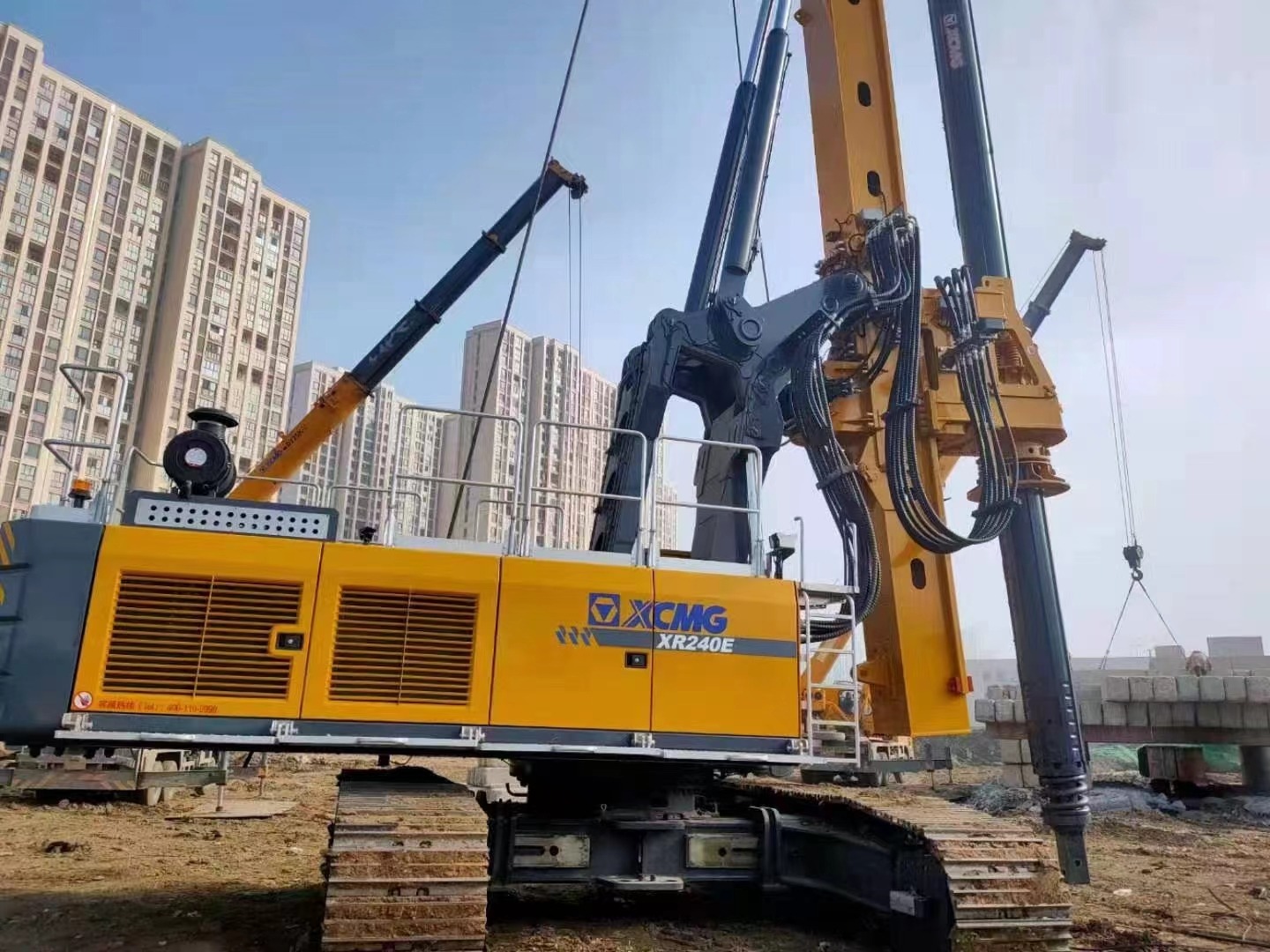
Piles are cylindrical members that penetrate deep into the soil or rock layer. The anti-slide pile in the slope treatment project transfers the slope thrust from the upper part to the lateral soil or rock mass at the lower part of the pile through the pile body, relying on the lateral resistance of the lower part of the pile to bear the downward thrust of the slope, so that The slope remains balanced or stable
Anti-slide piles are similar to general pile foundations, but they mainly bear horizontal loads. Anti-slide piles are also one of the most commonly used solutions in slope treatment projects. From early wooden piles to modern steel piles and reinforced concrete piles currently commonly used in slope projects, the cross-section types include circular and rectangular. Construction The methods include driving, mechanical hole forming and artificial hole forming. The structural types include single pile, row pile, pile group, anchor pile, and prestressed anchor cable pile.
Anti-slide pile types, characteristics, and applicable conditions
(1) Types of anti-slide piles
Anti-slide piles are classified according to material into wooden piles, steel piles, reinforced concrete piles, and composite piles.
Anti-slide piles are classified according to the method of pile formation, including driven piles, static pressure piles, and cast-in-place piles. In-situ cast-in-place piles are further divided into two categories: immersed cast-in-place piles and bored piles. Commonly used bored piles are divided into mechanically drilled piles and manually dug piles.
Anti-slide piles are classified according to their structural types, including single piles, row piles, group piles, and anchored piles. Common types of pile rows include chair-type pile walls, portal-type rigid frame pile walls, and row-frame anti-sliding pile walls (see Figure 2 ), anchor piles commonly include anchor rods and anchor cables. Anchor rods include single anchors and multiple anchors. Anchor cables and anti-slide piles mostly use single anchors.
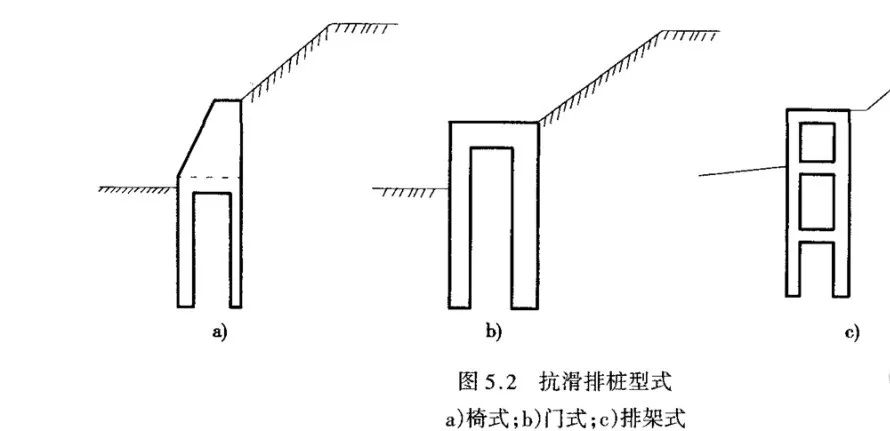
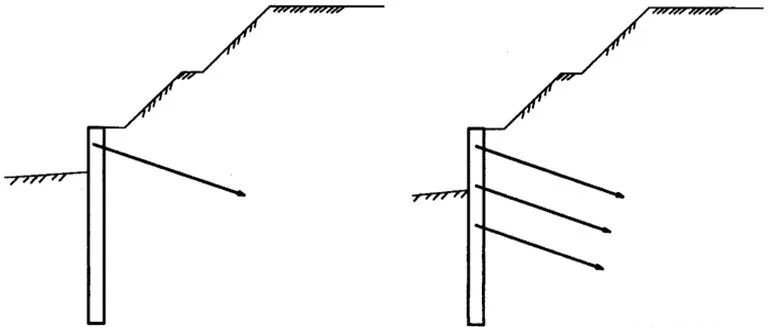
Anti-slide piles are classified according to the cross-section form of the pile body, including circular piles, square piles, rectangular piles, “I”-shaped piles, etc.
(2) Characteristics and applicable conditions
When driving anti-slide piles in construction, the impact of construction vibration on slope stability should be fully considered. Generally, fully buried anti-slide piles or filled slopes can be used, and the underlying strata should be drivable. In-situ cast-in-place piles are commonly used in the construction of anti-slide piles. Mechanical drilling is fast and the pile diameter can be large or small. It is suitable for various geological conditions. However, for slope projects with steep terrain, mechanical entry and erection are more difficult. In addition, water during drilling also affects the stability of the slope. The characteristics of artificial hole formation are that it is convenient, simple, and economical, but it is slow and labor-intensive. It is quite difficult to handle when encountering bad strata (such as quicksand). In addition, manual operation is difficult when the pile diameter is small. The pile diameter should generally be 1000mm. The above are suitable for artificial holes.
Monopile is the basic type of anti-slide pile and a commonly used structural type. It is characterized by simplicity and clear forces and functions. When the thrust of the slope is large and a single pile is not enough to bear the thrust or it is uneconomical to use a single pile, row piles can be used. The characteristics of the rack pile are large moment of inertia, strong bending resistance, small pile wall resistance, small pile body stress, and obvious advantages in weak strata. Anchors with anchor piles can use reinforced anchor rods or prestressed anchor cables. The anchor rods (cables) and piles work together to change the cantilever stress condition of the pile and the mechanism that the pile relies entirely on the lateral foundation reaction force to resist the landslide thrust, making the pile body The stress state and pile top displacement are greatly improved, making it a more reasonable and economical anti-slip structure. However, the anchoring end of the anchor rod or anchor cable needs to have better strata or rock formations. For anchor cables, it is even more necessary to have better rock formations to provide reliable anchoring force.
The anti-slide pile group generally refers to a combined anti-slip structure with more than 2 rows in the transverse direction and more than 2 rows in the longitudinal direction. It is similar to a pier or cap structure. It can withstand greater landslide thrust and can be used in special landslide control projects or special projects. Slope engineering for purpose.
2.1 General procedures
The construction of anti-slide piles mostly adopts mechanical drilling or artificial drilling, and on-site concrete pouring is used for construction.
Cast-in-place piles are an underground hidden project with high-quality requirements, and many construction procedures, and must be completed continuously in a short period of time. Therefore, construction should be carried out according to procedures. Prepare technical information, prepare construction organization design, and prepare for construction. The construction management system for each process should be established according to the design requirements, relevant specifications, procedures, and construction organization design. The construction, supervision, design and owner management, monitoring, technical services, and technical tracking are in place. Ensure that construction is carried out in an orderly, fast, and high-quality manner.
2.2 Selection of pile setting technology
The staking process is also called the hole-forming method or the hole-forming process. There are many types of cast-in-place pile construction, and the main type commonly used in anti-slide pile construction is non-squeezing cast-in-place piles. Only by selecting the piling technology correctly and appropriately can the construction quality and construction period be guaranteed.
2.3 Construction technology
- First lay out the pile positions and clear the platform position according to the design drawing. The excavation surface should be higher on the inside and lower on the outside to facilitate drainage.
- Manual pile digging and wall protection construction
① Measurement and positioning: Measure and place the axis according to the on-site coordinate points provided by the design, determine the four side piles of the pile body according to the axis, and then protect the side piles. The allowable deviation of the pile position is 10mm. Excavation can only begin after the supervisor has reviewed and accepted the project and completed relevant procedures.
② Construction of lock mouth: First, support the formwork according to the size of the hole, ensuring that the thickness of the lock concrete is not less than 40cm, and the lock concrete is 45cm higher than the original ground.
③ Pile excavation: Use a short-handled shovel and a hoe to dig in the clay layer; use a pneumatic pick to enter the sandstone layer; if it is difficult to construct with a pneumatic pick on solid rock, drill and blast construction are used.
④Transportation: Set up vertical transportation brackets on the pile holes, use winches as lifting and earth-moving equipment, and transport the lifted soil to the designated spoil site in a timely manner to avoid environmental pollution.
⑤ Wall protection construction: The wall protection concrete adopts mechanical mixing, manual pouring, and vibrator tamping methods. The slump is controlled at 8-10cm. The principle of excavation for one section and support for one section shall be adopted. The depth of excavation shall not exceed 2m, and each section shall be regarded as a construction cycle for downward construction. The protective wall is made of C20-reinforced concrete with a thickness of 20cm. Insert vertical steel bars between sections (25cm into the lower section) to improve the integrity of the protective wall. The templates are connected and fixed with clamps and fasteners to ensure rigidity. The protective wall concrete must be poured for 8 hours before the formwork can be removed.
⑥ The lighting in the pile uses 36V safety voltage, and the lighting bulbs in the holes use special waterproof bulbs to ensure safety.
⑦Safety measures: Pre-embed a ladder pendant at the lock. It is convenient to hang a foot ladder when the depth reaches a certain level. Construction workers must climb up and down the foot ladder when going up and down. A rainproof shelter should be built on the pile mouth, and a protective fence should be set up around the pile mouth. Ventilation must be ensured under the hole, and harmful gases must be detected at any time. Once harmful gases are found, construction workers must evacuate immediately and use ventilation to dilute the concentration of harmful gases. Construction can only continue after it is absolutely safe.
⑧Inspection: After the pile is completed, comprehensively measure the size of the pile body, the elevation of the hole bottom, the center line of the pile position, and the verticality of the shaft wall, and make construction records. After the supervisor and relevant quality inspection personnel jointly inspect and identify the holes one by one, and if the design requirements are met, the concealed project acceptance will be handled, and then the steel cages will be made, hoisted, and concrete poured.
9,The hole pile protection wall must meet the following requirements:
a. The thickness of the protective wall, the configuration of the lap bars, and the concrete must meet the design requirements.
b. After the hole pile is opened, the pile wall concrete should be poured as soon as possible, and the pouring must be completed all at once on the same day.
c. Do not pour concrete for wall protection when the formwork is flooded with water.
d. If honeycombs or water leakage are found on the protective wall, they should be blocked or diverted in time.
4). Blasting inside anti-slide pile holes
① Use an electric detonator to detonate.
② The blast hole must be drilled and blasting is strictly prohibited. The depth of the blast hole for soft rock should not exceed 0.8 meters, and the depth of blast hole for hard rock should not exceed 0.5 meters. The number, position, and diagonal insertion direction of blast holes should be determined according to the direction of the rock formation section. The center group should be focused on drilling the core, and the four sides should be inserted obliquely on the edges.
③Strictly control the dosage and focus on loosening. Generally, the center blast hole is loaded with 1/2 knot of nitramine explosives, and the side blast holes are loaded with 1/3 to 1/4 knot of explosives.
④ Use emulsion explosives if there are water holes, and try to avoid blind shots. If there are blind shots, they must be handled according to safety regulations.
⑤ The supports near the blast hole should be reinforced to prevent the support from being blown out and causing hole collapse.
⑥Smoke must be exhausted quickly after blasting in the hole. Measures such as putting an electric blower into the bottom of the hole to blow air can be used.
⑦Anti-sliding pile blast hole layout diagram
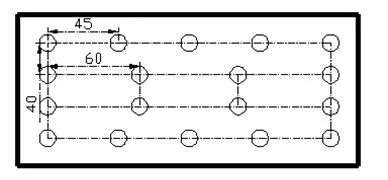
5).Reinforced cage production
The steel bar materials used must have a warranty and test report.
② When processing steel bars, the overlapping positions of the main bars should be staggered, within 35 days and not less than 500mm, and the number of joints within the range should not exceed 50% of the total stressed steel bar area. Welding of main bars must ensure that the overlap length is not less than the specified value. There are no joints for the longitudinal main reinforcement within 2m below the top of the pile. The horizontal reinforcing bars must be spot welded to the longitudinal bars to form a strong steel cage to ensure that the steel cage does not deform or twist.
③ Use 22# iron wire to tie all the stirrups and main bars. The tie should be firm and spot-welded appropriately.
6). Acoustic tube installation
① After the steel cage is tied, install the acoustic pipe. The acoustic pipe shall be a metal pipe with an inner diameter of not less than 40 mm and a thickness of not less than 3 mm. The acoustic tubes should be tied at the four inner corners of the steel cage, and the ties should be firm.
② The bottom of the acoustic detection tube is welded and closed with a thin steel plate. When the same acoustic detection tube is connected, it is welded with a steel casing. The upper end is closed with a wooden plug. There is no foreign matter in the tube, and the connection is smooth and watertight. The pipe opening should be more than 100 mm higher than the top of the pile, and the height of the acoustic pipe opening should be consistent.
7). Pile core concrete pouring
① Please ask the supervision unit to check and accept the pile of steel bars in the lower hole. Only after passing the inspection can the pile core concrete be poured.
② Before pouring, carefully check that the machine is in good working condition, the materials used meet the requirements, and the mix ratio of the mixing team is clear.
③Assign a special person to stand by and make records of the pouring of pile core concrete.
④ When mixing concrete, strictly follow the concrete mix ratio. The concrete mixing time should be no less than 90 seconds, and the slump should be controlled within the range of 8 to 10CM.
⑤ Dry pouring method is used for pouring: During the concrete pouring process, a string tube is used to ensure that the distance between the end of the string tube and the concrete pouring surface is no more than 2M to prevent the coarse aggregate and cement mortar from being separated and segregation. The pile core concrete is vibrated once every 0.3 meters with a plug-in vibrator to ensure the density of the pile core concrete. Each pile core must be poured continuously and no construction joints shall be left. After the pile core concrete is poured, sprinkle water for curing after 8 hours, and the curing period shall not be less than 7 days. When pouring core concrete for piles, prepare concrete test blocks, carefully maintain them, and submit them for inspection after reaching the age.
2.4Construction quality control
(1)General requirements
Anti-sliding piles are a projects with high-quality requirements, and the construction quality of sliding piles is directly related to the success or failure of the project. Therefore, controlling construction quality is particularly important. The principle of quality first must be adhered to during construction and comprehensive quality management must be implemented.
Anti-slide piles mostly use cast-in-place piles, and several key processes such as hole formation (including drilling and clearing holes), reinforcing steel cages, and concrete pouring must be carefully controlled. After each process is completed, quality inspection should be carried out in a timely manner. If the previous process is unclear, the next process cannot be carried out to avoid hidden dangers.
During construction, a full-time quality inspector should be assigned to each construction site to conduct comprehensive inspection and supervision of construction quality. Quality responsibility should be assigned to each person and every pile. The quality control of cast-in-place piles mainly refers to the quality standards and control methods of drilling, clearing holes, making and placing steel cages, concrete preparation, pouring, and other processes. It should be formulated based on the design documents and national or industry standards. Specific standards and requirements that are in line with engineering reality and easy to operate.
(2) Technical measures:
① Accurately measure the pile position, and release the guard piles (4) crosswise according to the center of the pile position, about 1.0m away from the edge of the hole. Always check pile hole clearance dimensions and flat position. Make the centerline error, cross-sectional size, and orifice plane position of the hole meet the design requirements.
② The overlap length of the upper and lower sections of the retaining wall shall not be less than 50mm. Each section of the retaining wall shall be continuously constructed on the same day. The concrete of the retaining wall must be dense. Use a quick-setting agent according to the geological conditions. The retaining wall formwork should be dismantled after 8 hours. The pile body reinforcement The joints are made according to the instructions in the reinforcement diagram.
③Concrete in the hole must be poured continuously at one time without stopping midway. After the pile holes are poured, the pile top concrete shall be cured promptly.
④ Strictly control the materials. The steel bars should have a factory quality guarantee or test report, and carry out mechanical performance tests. Conduct random inspections on the steel bars entering the site. Follow the principle of “test first, then use”. Seriously corroded and other non-standard steel bars should be inspected. Steel bars will be strictly prohibited from acceptance and use.
⑤ Strictly control the processing quality of steel bars, strengthen the storage management of processed steel bars, and ensure the quality of the binding and welding of steel bars.
2.5 Issues that should be paid attention to during construction
Safety requirements and prevention and control measures for pre-reinforced piles:
(1) The on-site technical person in charge shall conduct a comprehensive, specific, and targeted safety technical briefing to the construction team before construction, including the workplace and safety protection measures, safe operating procedures, and safety precautions, and conduct regular safety self-examinations, the use of manual lifting equipment is strictly prohibited.
(2) Hang safety signs at the construction site, especially at major construction sites, operating points and dangerous areas, and at major passages. Safety operating procedures for random installation of construction machinery and equipment.
(3) Before starting excavation, make preparations to prevent rockfall and landslides. First, remove the gravel and debris within 2m around the wellhead. When excavating on the surface of relatively broken soil, the wellhead must be supported and the lock should be higher than the wellhead. The ground surface is 0.45m. When working in pile foundation pits, you must wear a safety helmet.
(4) Measures for the collapse of the protective wall: Immediately after digging the 1-meter pile holes in each section, support the protective wall construction and pour concrete for the protective wall. The protective wall formwork can be removed after 8 hours. The upper and lower protective walls must be tied with steel bars, and the overlap length should not be less than 10cm. To prevent the protective wall from sinking due to its own weight due to quicksand and silt, appropriate anchor rods can be added to the protective wall in the broken section to prevent the protective wall from sliding down.
(5) All equipment, facilities, safety devices, tools, and labor protection supplies at the construction site need to be inspected frequently to ensure they are in good condition and used safely. Always check the quality of the earth-moving hanging basket and whether the hanging rope is firmly tied to prevent falling earth and rocks from injuring underground construction workers. Regularly check the quality of the hoist, pulleys, slings, etc. to prevent possible accidents such as breakage and falling off.
(6) If blasting is required for the excavation of pile holes, the control of blasting flying rocks requires covering the gun cover at the locking position.
(7) When the depth of the pile hole exceeds 8m, the ground is equipped with an air supply device into the hole, and the air volume is not less than 25L/S. When cutting the stone at the bottom of the hole, the air supply volume must be increased.
(8) Set up C20 reinforced concrete retaining walls in the pile holes, and send special personnel to regularly check the construction quality and deformation of the concrete retaining walls in the pile holes.
(9) The wellhead retaining ring should be 0.3m above the ground to prevent debris from the wellhead from falling into the pile hole and injuring personnel. A ladder must be placed in the pile hole and extended to the working surface as the depth of the hole increases. For safe use, construction workers must use ladders to get up and down. It is prohibited to use electric winches to carry people. It is strictly prohibited to operate under the influence of alcohol. Smoking and using open flames in the hole are not allowed.
(10) Manhole covers and fences must be installed for pile openings where concrete has been poured or holes are being dug but are not yet completed.
(11) After pumping water in the hole, the special power supply for pumping water must be cut off before the operator can work in the pile hole. Operation with a power supply is strictly prohibited. Digging personnel must use safety ladders when going up and down the well; tools needed underground must be delivered with special ropes. The ropes should be checked at any time and replaced immediately if any broken wires are found. Any good casting is prohibited. It is appropriate for underground workers to continue working for 2 hours, and the longest time should not exceed 3 hours. The underground workers should be replaced frequently and the downhole operations should be rotated. There are reliable communication links above and below the well, such as walkie-talkies. Workers who cooperate with the hole opening must pay close attention to the situation inside the hole and must not leave their posts without permission.
(12) The installation and removal of all power supplies and electrical lines in the construction site must be handled by a certified electrician. Electrical appliances must be strictly grounded, connected to zero, and use leakage protectors. The electricity used in each pile hole must be separated. It is strictly prohibited to use one gate for multiple holes and one gate for multiple purposes. “Three-phase five-wire” must be used. The overhead height of the wires at the construction site shall not be less than 3m from the ground and must be well insulated.
(13) After the pile hole is accepted, immediately hoist the pile steel cage into place. When hoisting the steel cage into the hole, it is necessary to prevent collision and damage to the hole wall.
(14) After the hole is formed and before concrete is poured, the wellhead should be covered with bamboo plywood or wooden boards, and safety warning measures should be provided.
Thanks